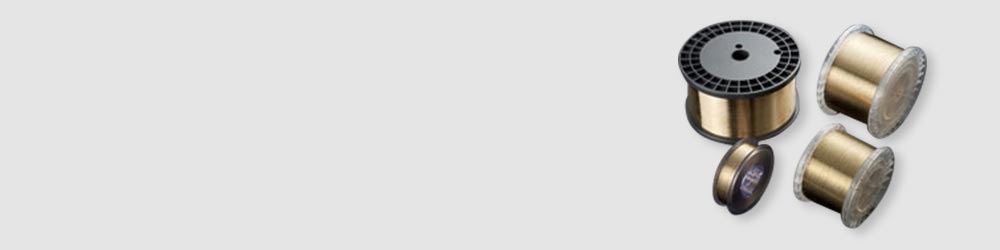
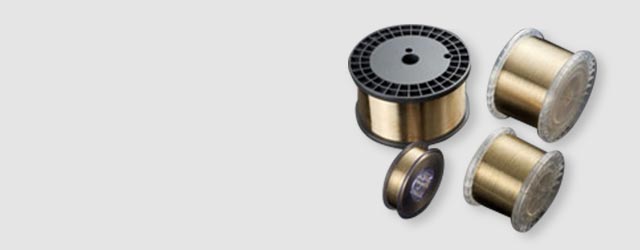
放電加工用
電極線に
ついてのQ&A
- 加工条件の設定方法は?
-
加工条件設定 <加工速度を上げるための条件>
例)三菱電機製ワイヤ放電加工機でのチューニング
●加工機メーカー別パラメータ
加工機メーカー 放電エネルギー設定 オフタイム設定 GFマシニングソリューションズ(旧アジェ) P、T TD GFマシニングソリューションズ(旧シャルミー) A、IAL B、Aj 西部電機 I OFF ソディック IP、ON MA、OFF ファナック ON OFF、SV 牧野フライス製作所 ピーク電流、ON OFF 三菱電機 IP SB、OFF ●参考:放電エネルギーをどれだけ上げられるかは、板厚の違いによって変わります。
板厚によって以下のように設定を見直すと、良好な加工条件が得られる可能性があります。板厚 設定ポイント 20mm以下 - ・一般に板厚が薄くなるにしたがって放電エネルギーも弱くします。
- ・薄板はエネルギーを大幅に上げられないため速度上昇は低めとなります。
- ・10mm以下では放電エネルギーを上げられる量もわずかです。
20~60mm - ・高圧噴流の状態がよければ加工効率が高まります。
- ・平プレート加工であれば、できる限りノズル密着状態としてください。
- ・加工スラッジの排出がよくなるので、さらに放電エネルギーを上げての加工が可能です。
60mm以上 - ・一般的には板厚が厚くなるほど、ワイヤは消耗し断線しやすくなります。
- ・ワイヤ速度を上げることにより加工速度を上げられる可能性があります。
- ・黄銅線との有意差が出やすい板厚であり、大幅な条件変更が可能です。
注:設定ポイントは、お客さまの加工条件等によって一品一様のため、お客さまの状況に合わせて、設定見直しをお願いします。
ご不明な点がありましたら、お問い合わせください。 - 加工条件の変更方法は?
-
加工条件の最適化 例)三菱電機製ワイヤ放電加工機の場合
●荒加工(1st-Cut)編
●加工条件の変更方法φ0.2ワイヤによるSKD-11、60t加工の場合 *目安表です。【AE:21ノッチ、SE:1ノッチ使用】
標準値 補正値 材料 SKD-11
焼入NAK/
HPM®SK-3/
S45Cステンレス鋼 アルミニウム 銅 超硬/
銅タングラファイト 電圧切替Vo (ノッチ) 12 0 0 0 0 0 0 +4 加工セッティングIP (ノッチ) 9 0 −1 0 0 −1 −1 −2 休止時間OFF(ノッチ) 1 0 0 0 0 0 0 0 安定回路A SA (ノッチ) 3 0 0 0 0 0 0 −2 安定回路B SB (ノッチ) 10 +2 +2 +2 +3 0 0 +4 ワイヤ張力WT (ノッチ) 8 0 0 0 0 0 0 −1 平均加工電圧VG (V) 39 0 0 +2 0 +8 +5 +15 実加工速度FA (%) 100 90 85 85 200 85 50 40 標準値 補正値 材料 SKD-11
焼入片ノズル
離れ両ノズル
離れ段差ワーク テーパー3度 テーパー5度 テーパー10度 テーパー15度 電圧切替Vo (ノッチ) 12 0 0 0 0 0 0 0 加工セッティングIP (ノッチ) 9 −1 −1 −2 0 0 −2 −2 休止時間OFF(ノッチ) 1 0 0 0 0 0 0 0 安定回路A SA (ノッチ) 3 0 0 0 0 0 0 −1 安定回路B SB (ノッチ) 10 +2 +2 −1 +2 +2 +3 +3 ワイヤ張力WT (ノッチ) 8 0 0 0 −1 −1 −2 −3 平均加工電圧VG (V) 39 0 +4 +4 0 +5 +5 +10 実加工速度FA (%) 100 80 60 60 90 85 70 50 *安定回路(SE)ノッチを1→2→3→4→5と上げるごとにワイヤ断線は発生しにくくなります。
●加工精度の改善について(パンチ形状の場合)
●加工面に筋が発生する場合
●仕上げ加工時のポイント(加工中のチェック事項)
- 不具合で困った時の対策は?
-
不具合と対策
トラブル名 トラブル状況 原因 チェック事項・解決方法 1 断線不良 ①給電板付近での断線 ・給電板が摩擦している 給電板のチェック、定期交換 ・給電板ノズルの水が給電板に当たっていない 給電板ノズル清掃、水圧チェック ②ワイヤガイド付近の断線 ・ワイヤガイドが汚れている 定期的なメンテナンスの実施 ・ワイヤガイドが押さえ力が強すぎる 最適押さえ力の調整 ・ワイヤガイドの位置精度がズレている 位置精度の再設定 ③空送り時の断線 ・線掛け不良 線掛け位置チェック ・ワイヤが混線している(モツレ・クグリ) ワイヤを交換または巻きをほどいてみる ④加工開始直後および5mm以内での断線 ・加工液に空気が混入している(気中断線) 加工条件が強すぎる 加工物の脱脂洗浄をする ・加工物が傾いている 加工液水圧をチェック
垂直出しを行ってから加工スタートする⑤5mm以上加工後の断線 ・加工液圧が低い 加工液ノズルの位置不良、摩耗チェック ・加工条件が合わない 加工液供給タンクの液吸い込み口の汚れチェック ・加工物内の異物、ピンホールがある 複雑形状加工の場合、加工液の逃げのチェック ・ワイヤ不良 ワイヤを替えてみる ・ワイヤの走行不良 ウレタンゴムローラーの摩擦、傷、汚れのチェック
ワイヤ張力の設定ミス調整2 加工精度不良 ①形状不良 ・ワイヤガイドの押さえ力不足、位置不良 ワイヤガイドの押さえ力、位置調整 ・ワイヤ張力不足 ワイヤ張力の適正設定 ・周辺温度変化が大きい 材料歪(応力)の除去 ・加工材料の不均一 ワイヤの垂直不良 ・オフセットが不適正 ガイドダイス等の清掃、メンテナンス 3 面精度不良 ①面が粗い ・加工条件が合わない(不均一放電) ワイヤ送りを速める ②加工面に縦スジが発生する ・ワイヤ張力不足 加工速度を速める ③加工速度変動が発生する ・加工速度が遅い イオン交換樹脂の交換および水比抵抗の安定化 ・イオン交換樹脂の劣化 ワイヤ走行系(ガイド系)の清掃、メンテナンス ・ワイヤの走行不良 給電子の消耗具合チェック・清掃、メンテナンス ・ウレタンローラーの摩擦、傷、汚れ ・ワイヤ張力不適正 4 加工速度不良 ①加工速度が上がらない ・加工条件が合わない 取説設定加工条件に合せてみる (材質、板厚、サイズの不適正) 上下ノズルの位置不良、摩耗チェック 5 カール不良 ①スクラップボックス内でワイヤが不規則に収納される
(ワイヤが暴れる、パーマネント状になる)・ワイヤの残留応力(ストレス)の不均一 印加電流値を1TAP上げてみる(加工速度向上) ・搬送ローラー・ベルトの偏摩耗 偏摩耗およびワイヤ径の1/3以上の摩耗で交換 ・搬送ローラー・ベルトの位置ズレ 加工機メンテナンス業者に相談 ・搬送ローラー・ベルトの押さえ力不適切 使用ワイヤに適合した押さえ力でワイヤ走行 ・ワイヤに大きな線グセがある 真直性のよいロットに交換してみる 6 自動結線不良(挿入不良) ①ガイダンスおよび下穴に自動挿入されない ・ガイダンスに汚れや詰りがある 定期的なメンテナンスの実施 ・下穴径(Work側)が小さすぎる 加工機のMin下穴径を確認する ・ジェット水圧・水量が低下している 手動にて水圧バルブを調整する ・上部ヘッドと下穴の位置ズレ プログラムのチェックおよび中心位置決めの実施 ・ワイヤに大きな線グセがある 真直性の良いロットに交換してみる 7 自動結線不良(切断不良) カッタ切断の場合 ・カッタの偏摩耗および切断力不足 ワイヤ痕があれば交換、切断押圧をチェック ①うまく切断できない ・ワイヤ切断端末にマクリができる 切断カッタを新品に交換 ②下穴に挿入されない ・ワイヤに大きな線グセがある 真直性のよいロットに交換してみる アニーラ切断の場合 ・ワイヤ径の入力ミス メーカー推奨ワイヤの材質・特性に合わせる ①うまく切断できない ・ワイヤ材質不適切 使用するワイヤ径を入力する ②切断位置が変わる ・ワイヤ質別違い 8 巻き不良(線クグリ) ①ワイヤ端末がくぐっている ・ワイヤ端末を離してしまう(人的要因が原因) 巻替え後の線クグリチェックの徹底 ②使用時は問題ないが、ボビン中程でクグリ発生 顧客側でのワイヤ端末取り扱いの徹底(ボビンを加工機にセットするとき) 9 巻き不良(巻き緩み) ①巻きが緩く、ワイヤが遊ぶ ・巻張力の調整ミス(ダンサーの不安定) ワイヤ径ごとの巻き張力に設定する ・巻替機の振動による遊び 据え付けをしっかりする ・巻替機でのボビンの変芯 ボビン形状および巻替機へのセット状況確認 10 巻き不良(偏巻き) ①ボビン鍔部で偏巻き(山・谷)がある ・巻替機のトラバーサ調整ミス トラバーサの調整および巻替時の定期チェック ・ボビンの変形 リターン制御モーターの変更 トラバ-スプ-リを極力巻き胴径に近づける ボビン形状のチェック
お問い合わせはこちら
- 電線統括部
- お問い合わせフォーム